镁碳砖是日本作为电炉应用而开发的,首次应用在转炉镁碳砖价格的实验在1970年开始的,经过6年正式推广使用,1977年川崎钢铁公司在转炉炉底和风口首次使用树脂结合的镁碳砖,开创了含石墨的复合耐火材料在转炉应用的先例。沥青结合的镁碳砖由西欧兴起的,通常的镁碳砖是有镁砂和鳞片状石墨中作为结合剂添加了热固性树脂,加入或不加防氧化剂的不烧砖。近几十年来,由于日益苛刻的冶炼条件和不断变化钢铁冶炼生产技术,对镁碳质耐火材料提出了较高的要求,主要集中在改进工艺,提高质量和使用效果,并已取得了良好效果。下文是镁碳砖原材料的选择,供参考!
为验证该防氧化涂料的实际使用效果,我们在三个钢厂分别进行了现场试验。采用钢包渣线镁碳砖的局部涂刷和侵蚀最严重处的整体涂刷两种方式,来评价防氧化涂料起到的作用。局部涂刷的现场,观察钢包烘烤结束后渣线镁碳砖的外观,测量钢包下线后涂刷部分的残余厚度,对比未涂刷涂料且与涂刷涂料部分处在相同使用环境的渣线镁碳砖残余厚度(结果见图4和图5)。侵蚀最严重处整体涂刷的现场,新砌钢包烘烤时间为120小时,高烘烤温度1000℃,选定侵蚀最严重的部位作为研究对象,对比涂刷前后该处镁碳砖残余厚度和使用寿命。
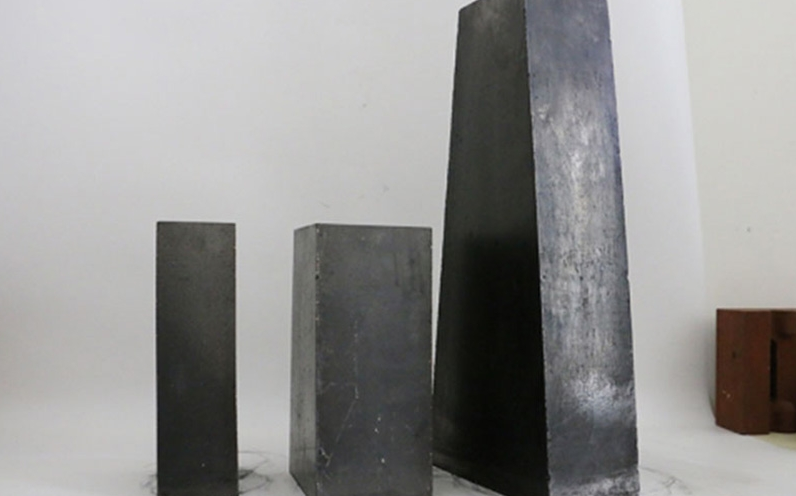
出了不同碳源对试样经不同温度处理后常温耐压强度的影响。可以看出,与200℃热处理后各试样的常温耐压强度相比,经埋碳保温处理后,其他温度处理后试样A1、A2、A3的耐压强度都出现大幅度降低,随着温度的提高,各镁碳砖试样的耐压强度又逐渐有所升高。这是由于酚醛树脂在200℃时固化,此时主要靠树脂本身提供强度。但在热处理过程中,树脂发生分解,释放H2O、CH4、CO2等气体,气体的大量挥发会产生气孔,导致试样的显气孔率增大,致密度下降,强度下降。此时试样强度的大小由树脂残碳和炭素原料所形成的碳结构所决定。但温度为1200及1400℃时,基质会发生烧结使试样致密度提高,试样的显气孔率也出现下降,强度随之开始升高。在经过埋碳热处理后,试样A3均具有高强度,这主要和沥青本身具有黏结作用有关。镁碳砖厂家
各试样高温抗折试验后试样基质的XRD图谱见图4。由图4可知:3个试样中均含有方镁石、镁橄榄石以及少量的Si C和C。高温抗折试验后试样断面的显微结构照片见图5。可以看到:试样A1中生成较多发育良好的柱状晶体,根据物相组成并结合微区成分分析判断是镁橄榄石,还有一些空心管状物,根据文献可以判断主要是树脂裂解生成的碳管或碳洋葱,粒状晶体为碳化硅;试样A2中存在较多棒槌状晶体,根据物相组成和结合微区成分分析,判断主要是发育不完全的镁橄榄石,管状物为碳管或纳米碳管,粒状晶体为碳化硅;而试样A3同时存在着大量的长度较长的发育不完全的镁橄榄石及碳管或纳米碳管,值得注意的是还有数量较多的Si C纤维生成,可以推断是由液-气或固-气反应形成;而试样A1、A2中未见纤维状Si C,而呈粒状,可以推断是由液-固或固-固反应形成。镁碳砖